Food traceability
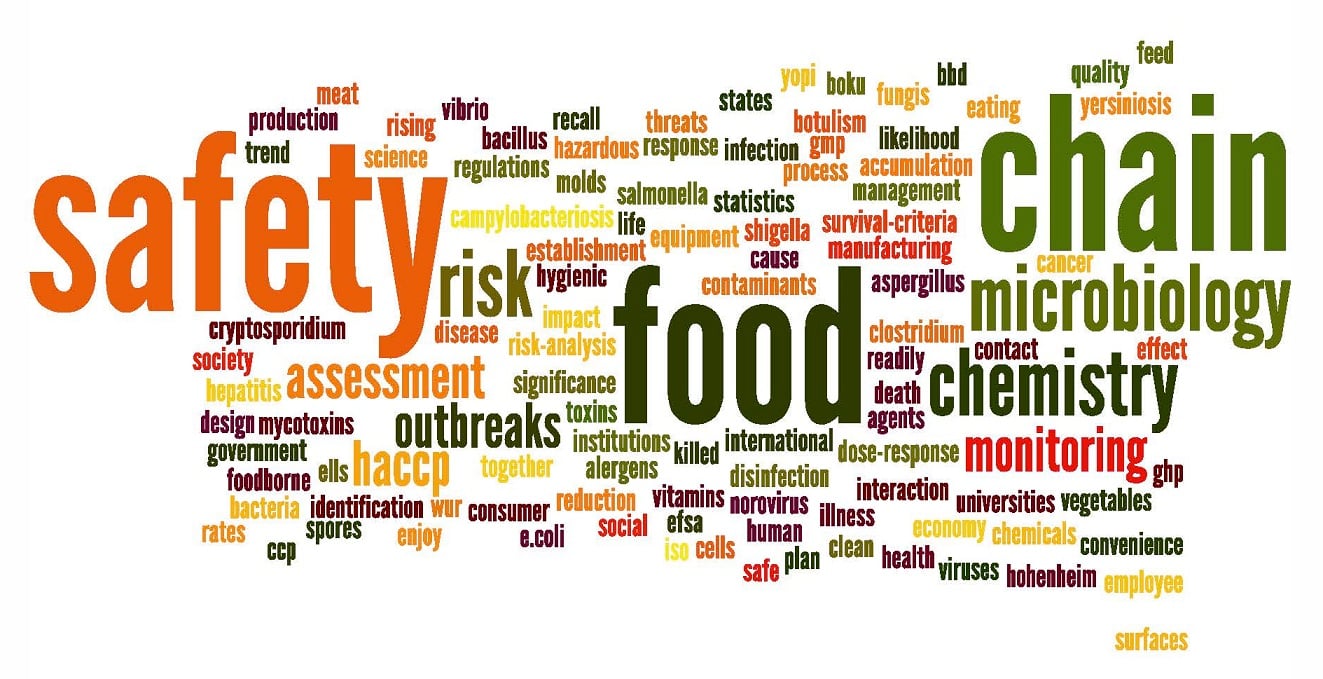
The 4 major benefits of tracking & tracing systems
The benefits of tracking and tracing tools
The food and beverage manufacturing industry faces challenging market conditions on multiple fronts: product safety requirements, thin margins, unique customer orders and constantly varying stock keeping units. In order to meet such challenges, manufacturers turn to tracking and tracing tools. Capable of tracking materials and products within a single plant or throughout a network of plants, these tools have the potential to provide a range of benefits and competitive advantages.
Food and beverage manufacturers have traditionally relied on manual data collection methods to provide a best estimate on product and ingredient tracking, with reports based on paper records kept in filing cabinets. Automated systems, however, are providing manufacturers with access to dramatically more reliable real-time information. Such technology enables manufacturers not only to meet regulatory demands but also to respond more effectively in product recall situations—tracking products faster, more accurately, more efficiently, and more cost effectively. This also helps manufacturers establish brand value and provide a quantifiable return on investment.
1: Improved data collection and reporting
With the growing importance of food safety (allergens, gluten, ferment...) and EU/US Food Law’s, documenting details of your procedures for years and years has become impossible with a manual solution. An automated solution allows the user to collect data more effectively and with increased accuracy.
Afterwards it can be integrated with supply chain management, giving manufacturers access to more reliable and accurate information which allows them to:
- Track details of all stages of production
- Intervene during production when the collected data exceeds
the preprogrammed alarm limits - Identify the sources of ingredients used in or allocated for food production
- Identify businesses to which products have been supplied
- Adequately label or identify products
- Make tracing information available to authorities on demand
The automated data collection results in the improvement of the quality of produced goods and a reduction of the overall production cost.
Thanks to the track & trace systems it becomes a lot easier to respond to affected batches.
When for example a supplier needs to recall a certain ingredient, it becomes a lot easier for a manufacturer to deal with the recall. With a paper system or even worse, without a track & trace system, such recalls become financial and time-consuming nightmares.
2: Enhanced supply chain
A well-implemented automated product tracking and tracing solution provides a view into the key details of production throughout the supply chain, allowing manufacturers to respond better to demands at the retail end of the food and beverage manufacturing supply chain. To reduce extra inventory held in stockrooms, for example, many retail outlets are looking for manufacturers to ship just enough product to replenish their shelves. In an increasingly competitive market, food manufacturers without the ability to respond to such demands risk losing valuable contracts.
However, to schedule production and get the product there on time, food manufacturers require real-time information on variables such as current production status, what is being manufactured, how much has been produced, and where it is in the shipping process. Automated track and trace solutions allow production tracking through each manufacturing area, supplying the key data to make informed decisions.
3: Increased inventory accuracy
Food and beverage manufacturers are also working to reduce costs and increase efficiency related to inventory. These continuous improvement processes are focused on carefully measuring and managing raw materials while maintaining control over the inventory of finished goods. Track and tracing systems can be used to monitor and record actual usages in real time, enabling far more precise inventory control compared to manual systems.
Additionally, automated tracking and tracing solutions can track the amount of actual material used at each manufacturing stage and can automatically deduct from inventory levels in business systems. This enables manufacturers to track inventory levels in real time and order only the amount of raw material needed, which eliminates the need for extra stock and reduces operating expenses.
4: Reduced costs
The data collected through a tracking tool provides a more complete view of the actual cost to manufacture each product by identifying the costs for each step in the production process, including:
- Actual amount of raw materials used
- Output from conversion processes
- The quality of the goods produced
- Amount of scrap
- Labour costs involved in each process step
- Equipment performance (efficiency, downtime, cycle time, production rate)
Using the collected data to examine specific costs associated with production areas can help business leaders making decisions that will reduce manufacturing costs and help them gain insight in their production process.
Succeeding in today’s competitive food and beverage manufacturing industry means ensuring that consumers can consistently rely on a finished product’s taste, texture, shape, and smell. From batch to batch and facility to facility, products under the same brand banner must maintain the same high standards and qualities. Failure to do so can result in uneven or declining sales and damage to valuable brand equity.
Implementing a track and trace system in the food and beverage industry does not only help manufacturers comply with the growing food safety requirements, it also increases their revenue, control over their production and decreases operational costs.
Yitch has already implemented tracking & tracing systems at multiple sites, providing both the hardware and software.
Source: www.foodqualityandsafety.com